When it comes to enhancing metal surfaces, electroplating offers a range of options to improve both appearance and durability. Two popular methods are nickel plating and chrome plating, which can be further classified into nickel-chrome plating and hard chrome plating. In this blog, we’ll explore the differences between these methods, helping you decide which is the best option for your project.
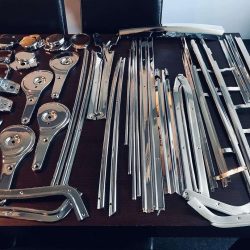
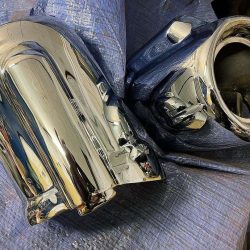
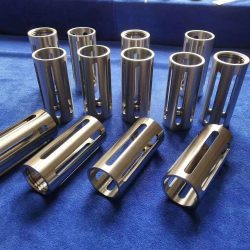
Understanding Nickel Plating
Nickel plating involves applying a layer of nickel onto a metal surface, providing a smooth, slightly yellowish finish. It is commonly used for its decorative appearance and functional properties.
Aesthetic Appeal
Nickel can mimic the look of silver, making it a cost-effective alternative for decorative applications.
Corrosion Resistance
Nickel provides decent protection against rust and corrosion, although it is less resistant than chrome plating.
Versatility
Suitable for a variety of metals, including steel, brass, and copper.
Why Choose Nickel Plating?
Cost-Effective
Nickel plating is typically less expensive than chrome plating, especially for small parts using barrel plating.
Specific Requirements
Some applications benefit from nickel’s properties, such as electrical conductivity or specific hardness needs.
Aesthetic Preference
Some clients prefer the warm, silver-like look of nickel over the bright finish of chrome.
SOME GLIMPSE OF OUR NICKEL ELECTROPLATING SERVICES
Diving into Chrome Plating: Nickel-Chrome vs. Hard Chrome
Chrome plating is divided into two main types: nickel-chrome plating and hard chrome plating. Each serves a distinct purpose depending on the desired function and appearance.
Nickel-Chrome Plating
Nickel-chrome plating involves a base layer of nickel with a thin top layer of chromium. This combination offers the best of both worlds:
Appearance
The chromium layer adds a bright, mirror-like finish with a bluish tint, making it more reflective than nickel alone.
Corrosion Resistance
The addition of chromium provides excellent protection against rust and corrosion, making it ideal for outdoor use.
Durability
Although not as hard as hard chrome plating, nickel-chrome offers a solid balance between aesthetic appeal and functional protection.
Applications of Nickel-Chrome Plating
Automotive Parts
Frequently used on bumpers, rims, and trims for its aesthetic and protective qualities.
Household Fixtures
Commonly applied to faucets, showerheads, and handles for a shiny, corrosion-resistant finish.
Motorcycles and Bicycles
Popular for decorative and durable plating on components exposed to the elements.
SOME GLIMPSE OF OUR NICKEL CHROME ELECTROPLATING
Hard Chrome Plating
Hard chrome plating focuses primarily on performance rather than appearance. Unlike nickel-chrome, hard chrome plating uses a thick layer of pure chromium, with no nickel undercoat.
Purpose
Hard chrome is designed for industrial applications where surface hardness, wear resistance, and low friction are key requirements.
Appearance
Unlike the decorative nickel-chrome finish, hard chrome has a dull, grayish appearance.
Durability
Hard chrome offers exceptional hardness and is often used in hydraulic systems, cylinders, and friction-based machinery.
Applications of Hard Chrome Plating
Industrial Components
Hydraulic rods, piston rings, and other parts subject to high friction and wear.
Heavy Machinery
Used on components that require maximum surface hardness for extended durability.
Friction-Based Uses
Ideal for parts in constant contact, reducing wear and tear.
Comparing the Three: Key Differences
Nickel Plating
- A warm, slightly yellowish finish that resembles silver.
- Offers decent protection but less resistant than chrome plating.
- Adds some hardness but is less durable than chrome plating.
- Generally more affordable, especially when using barrel plating.
Nickel-Chrome Plating
- A bright, reflective surface with a bluish tint.
- Excellent protection against rust and corrosion, perfect for outdoor use.
- A solid balance of hardness and corrosion resistance.
- Higher cost due to the addition of the chromium layer and rack plating requirements.
Hard Chrome Plating
- A dull, industrial look, focused on function over aesthetics.
- Good corrosion resistance but more specialized for industrial, high-wear environments.
- Maximum hardness, ideal for friction-heavy industrial uses.
- Typically reserved for industrial applications, with higher costs due to its specialized nature.
Why Clients Choose Nickel Plating
For clients looking for cost-effective solutions, nickel plating is often the go-to choice. It’s affordable and provides a pleasing finish, especially for smaller parts that can be plated using barrel methods. In contrast, nickel-chrome plating is perfect for applications that require both decorative appeal and corrosion resistance. On the other hand, hard chrome plating is ideal for heavy-duty industrial parts where durability and wear resistance are the top priorities.
Conclusion
The choice between nickel plating and chrome plating (nickel-chrome or hard chrome) depends on your specific project needs. If you’re seeking a decorative finish with excellent corrosion resistance, nickel-chrome plating is your best bet. For industrial applications that require maximum durability and hardness, hard chrome plating will meet your requirements. And for a more budget-friendly solution, nickel plating provides a reliable alternative.
At NK Electroplating, we specialize in all three types of plating—whether you need aesthetic appeal or industrial-grade performance, we’ve got you covered.
Explore More:
- Learn more about our Nickel Electroplating.
- Explore our Chrome Electroplating services.
- Discover the benefits of Hard Chrome Electroplating.
For personalized advice or a quick quote, contact us today!