When it comes to protecting machinery parts from corrosion and wear, choosing the right type of plating is crucial. In the world of plating, zinc and nickel are two of the most commonly used options, each offering its own advantages and disadvantages. But which is the best for your machinery parts? Let’s break it down.
The Basics of Zinc and Nickel Plating
Zinc plating is primarily used for its corrosion-resistant properties. It is often applied in thicker layers for machinery parts and works as a sacrificial coating, meaning it corrodes over time to protect the underlying metal. Zinc plating is not known for its aesthetic appeal but offers long-lasting protection, especially when thick coatings are applied.
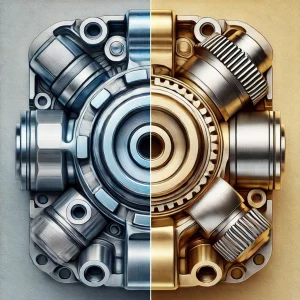
Nickel plating, on the other hand, is more about aesthetics and hardness. Nickel can offer a bright, stainless-steel-like finish and good corrosion resistance, but its true strength lies in its wear resistance. Nickel plating is more expensive than zinc and is often applied in thinner layers on machinery parts due to budget constraints, which can compromise its corrosion resistance.
Why Zinc Plating Is More Corrosion Resistant for Machinery Parts
When cost is a consideration, zinc plating often outperforms nickel plating in terms of corrosion resistance for machinery parts. This is especially true when thicker coatings are required. Here’s why:
Thicker Coating at a Lower Cost: Zinc plating can be applied in much thicker layers at a fraction of the cost of nickel plating. For instance, zinc plating starts at 25 INR per kilogram (as of 2024), while nickel plating costs range between 70-100 INR per kilogram. At these lower prices, nickel plating is applied in thin layers, making it less effective for long-term corrosion protection. However, zinc can be applied in much higher microns for the same budget, offering better corrosion resistance over time.
Sacrificial Protection: Zinc plating sacrifices itself to protect the underlying metal, meaning it corrodes first before the base material is affected. This sacrificial behavior helps to extend the life of machinery parts, especially in harsh environments. Even when zinc plating starts to wear off, it continues to protect the bare metal underneath.
Moisture and Corrosion: Nickel plating, while corrosion-resistant in itself, can sometimes trap moisture beneath the surface, leading to internal rusting of the underlying metal. This results in faster corrosion compared to zinc, which doesn’t trap moisture in the same way.
Wide Range of Colors: While zinc plating offers four different passivation colors (clear/blue, iridescent yellow, olive/military green, and black), nickel plating for machinery parts typically doesn’t come in color variants. Although black nickel is available, it’s purely decorative and not functional. Zinc’s passivation options provide added flexibility for customization based on different applications.
Nickel and Nickel-Chrome: Ideal Only With Higher Micron Coatings
While zinc plating excels in corrosion resistance, nickel or nickel-chrome plating becomes a competitive option when high microns of nickel are applied. This is commonly seen in automotive parts where clients can afford the thicker coatings, resulting in enhanced corrosion protection, superior wear resistance, and aesthetic appeal.
Nickel Chrome’s Aesthetic and Durability: Nickel-chrome, which consists of a base of nickel with a top layer of chromium, offers the best combination of hardness, wear resistance, and a shiny, steel-like appearance. However, this comes at a much higher cost and is typically reserved for high-end applications.
Wear Resistance of Nickel: Nickel plating excels in environments where wear resistance is critical, such as in hydraulic systems or high-friction parts. In contrast, zinc is less wear-resistant but is sufficient for many machinery parts that don’t require the same level of hardness.
Zinc vs Nickel: Final Recommendation
For those working with machinery parts, choosing between zinc and nickel plating comes down to a balance between cost, corrosion resistance, and aesthetic appeal.
Zinc plating is the better choice for parts that need strong corrosion resistance on a budget. It’s more cost-effective for thick coatings and offers sacrificial protection that keeps your machinery parts safe over the long term.
Nickel plating, and especially nickel-chrome, is ideal for parts where aesthetics and wear resistance are more important. However, to achieve the best corrosion protection, higher microns of nickel must be applied, making it a more expensive option.
When budgets are tight, and corrosion resistance is the primary concern, zinc plating is often the smarter choice. For more advanced applications where appearance, hardness, and wear resistance are equally important, investing in high-micron nickel or nickel-chrome plating may be the way to go.
Explore Our Services
At NK Electroplating, we offer a wide range of plating services for machinery parts, including zinc plating, nickel plating, and nickel-chrome plating. With our state-of-the-art equipment and expertise, we ensure that your parts get the exact protection and finish they need, no matter the application. For more information, visit our website or contact us today.